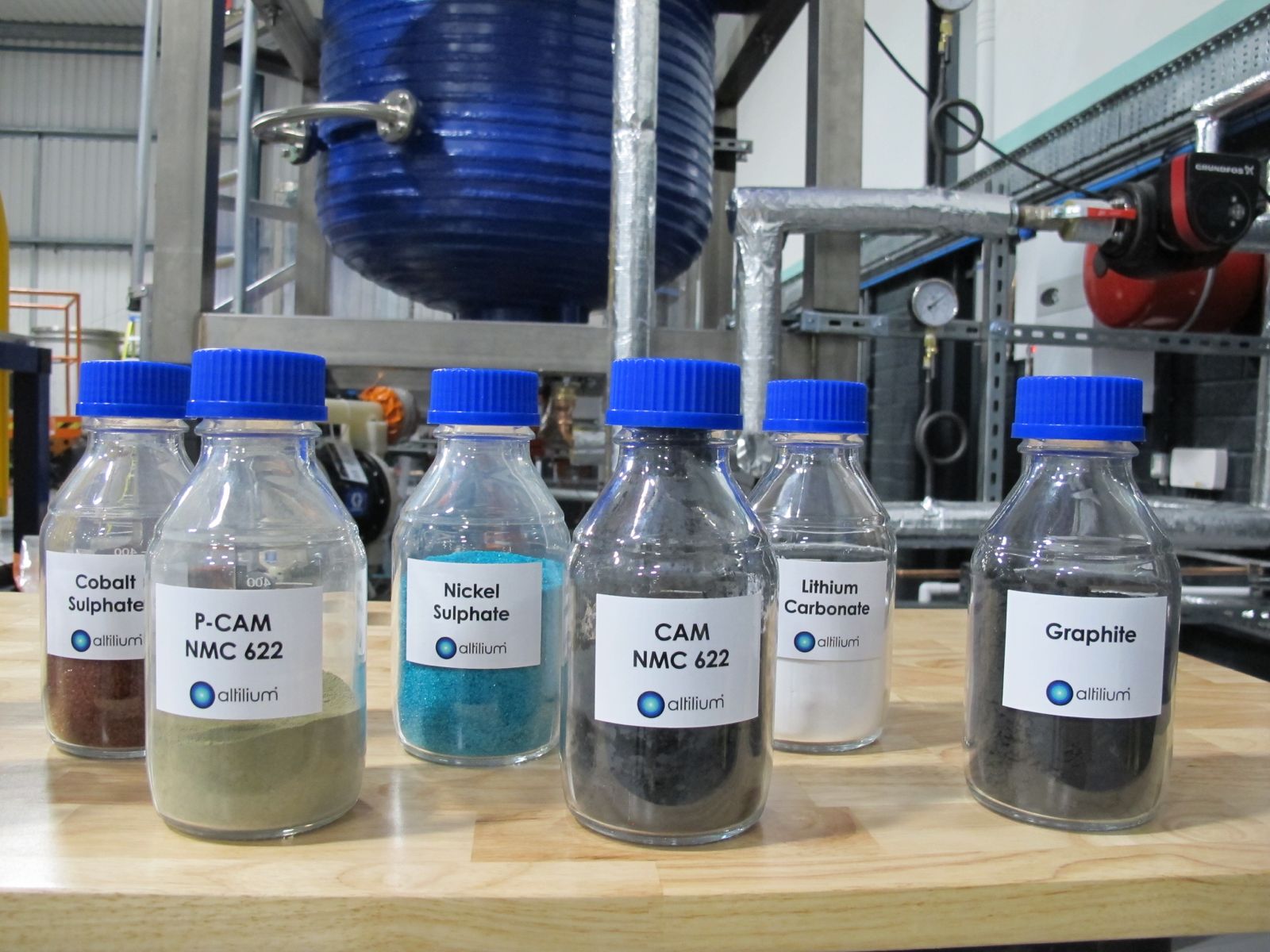
UK’s Altilium starts construction of new recycling plant
UK-based clean technology company Altilium has started construction of the country’s first at-scale EV battery recycling plant with integrated chemical refining capabilities.
The so-called ACT 3 scale-up plant, located in Plymouth, southwestern England, will serve as a blueprint for its planned ACT 4 “mega-scale” refinery later this decade. Once operational, ACT 3 will recycle materials from 24,000 EVs per year, which is the equivalent of 8,000 tonnes/year of black mass, Kallanish learns.
The 4-acre site will produce nickel mixed hydroxide precipitate (MHP) and lithium sulphate. It will also recover graphite, though specific volumes are yet to be confirmed. Global engineering consultancy Hatch is completing the engineering design work, and commercial operations are slated for Q4 2026.
“Our ACT 3 site marks the next phase in Altilium’s mission to close the loop on battery materials here in Britain,” explains chief operating officer Christian Marston. “This is about taking a strategic and incremental approach to scaling a vital new industry, one that ensures value stays in the country and creates long-term skilled green jobs.”
Altilium is taking what it calls a “structured, risk-managed” scale-up pathway to commercialisation. It already operates a technology centre where it developed its proprietary EcoCathode process, and a pilot line that processes one EV battery per day, validating the process and materials with automotive OEMs. At ACT 3, it will produce intermediate battery materials ahead of planned salts, precursor material and CAM production in ACT 4.
The company had previously intended to bring its ACT 4 refinery online by 2026, but its timeline has been revised. The plant, to be located in Teesside, is planned to process scrap from over 150,000 EVs, producing 30,000 t/y of cathode active materials (CAM). Altilium says the refinery will meet around 20% of the UK’s expected needs by 2030 and be one of the largest such facilities in Europe.
Like many other Western countries, the UK is currently dependent on critical battery materials imports. The UK Critical Minerals Intelligence Centre (CMIC) estimates that the country could need as much as 40% of the current global lithium production and 30% of the global graphite production by 2030 to feed its domestic battery sector. That is, however, if planned projects materialise.
To date, battery recycling in the UK has primarily focused on shredding batteries and black mass production, which is later exported for further refining. A report published by the Department for Business and Trade shows two battery recycling plants are operational in the UK, one by R.S. Bruce and one by S.A.R. Metals. Altilium stands out as the largest project alongside three other plans by Veolia, Glencore and Fenix Battery Recycling.
“The UK lacks commercial hydrometallurgy process capability. By scaling up its refining capacity, Altilium is reversing this trend, ensuring valuable battery metals remain in the UK supply chain,” an Altilium spokesperson adds.
Truly global, user-friendly coverage of the steel and related markets and industry that delivers the essential information quickly while delivering on most occasions just the right amount of between-the-lines comment and interpretation for a near real time news service of this kind.
Anonymous
Very good overview of the weekly steel market.
Anonymous